Our #TECH_Newser covers ‘news of the day’ #techNewserTechnology content.
| cutline • press clip • news of the day |
How sustainable biofuel will power the next generation of rockets | Aerospace Testing International.
By Paul Willis
During March this year bluShift Aerospace, a space rocket startup based in the US state of Maine, released footage of the first full-scale test of its hybrid engine.
‘)
}
// –>
The partial power test lasted only five seconds. It was preceded a year earlier by a test flight of a scaled version of bluShift’s Stardust rocket. The test flight saw the rocket fired a mile into the sky in the depths of the Maine winter, before parachuting safely to Earth. It was the first ever commercial rocket launch powered by a bio-derived fuel.
Sascha Deri, bluShift’s founder, has remained tight-lipped about the feedstock for the biofuel, revealing only that he discovered it during a visit to his brother’s farm and that the solid fuel is widely available worldwide and is completely non-toxic.
To prove the non-toxicity Deri has even eaten the fuel. “Calorie-wise it has no benefits to humans, it just passes through you,” says Deri. “But, hey, I’m still here!”
Green credentials
BluShift isn’t the only startup developing a biofuel powered rocket. Scottish launch company Skyrora is developing a rocket engine powered by kerosene produced from plastics waste. In 2020 it completed a test flight that reached an altitude of 16 miles from the Langanes Peninsula, Iceland.
Artist’s impression of the Skyrora XL, which is expected to launch for the first time early next year (Image: Skyrora)
UK-based propulsion engine maker Reaction Engines last November announced a partnership with the UK Government to develop a biofuel engine powered by cracked ammonia. But many are asking if a shift to biofuels is even necessary when space flight represents such a tiny proportion of aeronautical activity.
Filippo Maggi, associate professor of aerospace engineering at Politecnico di Milano in Italy believes the changes are worthwhile, not least because of the anticipated growth in space flight. This could increase the environmental impact of the launch industry.
“If you look at the business plans of these companies that are talking about continuous launches, it is going to be a little challenging from an environmental viewpoint,” says Maggi.
Virgin Galactic, for example, initially planned to send groups into space every 32 hours. The growth in small-scale satellites, known as cubesats and space tourism is also fueling an unprecedent-ed demand for more cost-effective launch services.
Even with the growth in space travel factored in, the predicted greenhouse gas emissions from space activity is less than that of most other industries. Of more concern believes Maggi is polluting the stratosphere with contaminants. These can take many years to clear and may lead to ozone depletion.
Putting real world impacts aside, shifting to biofuels also has symbolic value. “From the environmental viewpoint you are not changing anything dramatically, but you are planting a flag,” says Maggi. “And the space community wants to be seen as the community that makes this kind of effort.”
Sustainability responsibility
Deri’s interest in biofuels is part of a commitment to sustainability that began with altE Store, a US distributor of renewable energy products that he founded in 1999 and which now has an annual turnover of nearly US$30 million.
He launched bluShift in 2014 in his home state of Maine after discovering that the local government was offering grants and funding for aerospace companies.
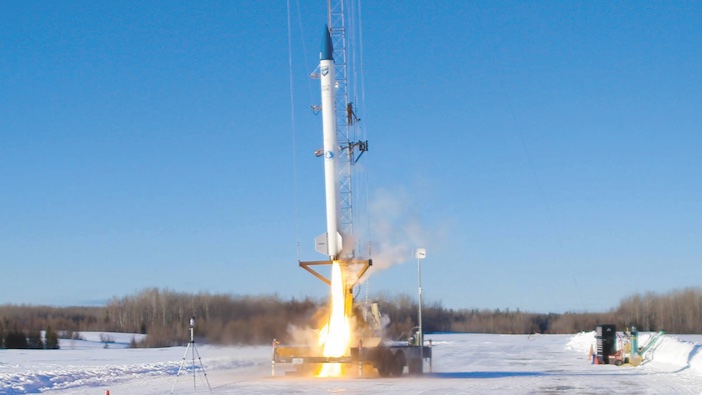
bluShift successfully launched a prototype rocket from Maine in January 2021 (Photo: bluShift)
“The night skies are very clear in Maine and growing up here I developed a strong curiosity about the universe,” says Deri, who has a bachelors in physics. “In a way it has come full circle for me as I get to fulfil the passion I had as a kid but do it in a way that is fundamentally more Earth-responsible.”
In the six years between bluShift’s launch and their first sub-orbital flight, Deri and his team spent close to four years refining the fuel recipe.
Once they were happy with the fuel mix a further 18 months was spent “getting the engine technology to work right”, Deri says. After that, they had just nine months to build the pro-totype rocket, find customers to offset the cost of the launch, find a launch site, obtain the necessary permissions and build a launch rail system.
The rocket’s engine is hybrid, which means that it uses a mix of solid and liquid fuel. This contrasts with most space rocket engines which typically use a mix of liquid propellants, often refined kerosene known as RP-1, which is combined with an oxidizer such as liquid oxygen (LOX).
“The solid fuel is on the inside of the combustion chamber and the oxidizer is a liquid. It burns from the inside out,” says Deri.
Unlike many rocket fuel propellants the fuel is extremely stable, says Deri.
“It takes some effort to get it going but just like a wood fire, once you get it going and open up the entry points of oxygen, it burns very nicely.”
Safety and cost
The stability of the fuel offers several advantages, not least of which is safety.
“It is really hard for a hybrid rocket to blow up because you have two different states of matter – a liquid and a solid – and the solid has a really hard time atomizing. So the moment you cut off the oxygen, the engine just shuts down.”
The stability of the fuel mix also significantly cuts down on R&D costs, says Deri, since “you don’t need all the precautions you need when you’re dealing with refined kerosene.” Their development costs are further lowered by using a non-cryogenic oxidizer.
He says, “If you look at our competitors they are spending at bare minimum twice what we have spent, and it is probably more like 10 to 20 times, to get to where we are today.”
However, compared to traditional fuel mixes Deri’s biofuel mix has a much lower specific impulse – the measure of how much thrust can be produced in relation to volume. As a re-sult, bluShift’s engine needs to be much larger to generate enough power to propel itself into orbit. The result is a much bulkier rocket for the same size payload.
“It’s like building a minivan to go to space as opposed to a Formula One racing car,” says Deri. “It is going to cost us a whole lot less to build.”
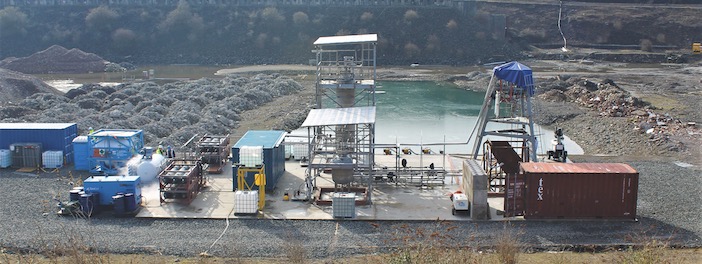
Skyrora’s engine test site in Scotland consists of a fuel and oxidiser loading system and pressure supply system to feed fuel to the engine on the test stand (Photo: Skyrora)
Transparent fuel
Other startups are being more transparent about the ingredients of their biofuel. Skyrora’s kerosene fuel mix is called ecosene and is made from four different plastics: high and low density polyethylene, polypropylene, and polystyrene.
The waste plastics undergo three stages to create the kerosene. Pyrolysis creates an oil-based sludge, hydrotreatment distils out different fuels and gases and then it is refined. Unlike bluShift, Skyrora’s biofuel closely resembles RP-1 grade kerosene and has not influenced the design of the propulsion system. However, their choice of propellant has changed the design of the engine.
“We have chosen high test peroxide [HTP] as our oxidizer, meaning we have to decompose it to water and oxygen,” says Jack-James Marlow, head of engineering UK at Skyrora.
“This process uses a catalyst and releases heat. We can use this heat to start the combustion process, meaning we do not need a separate igniter system like most engines.
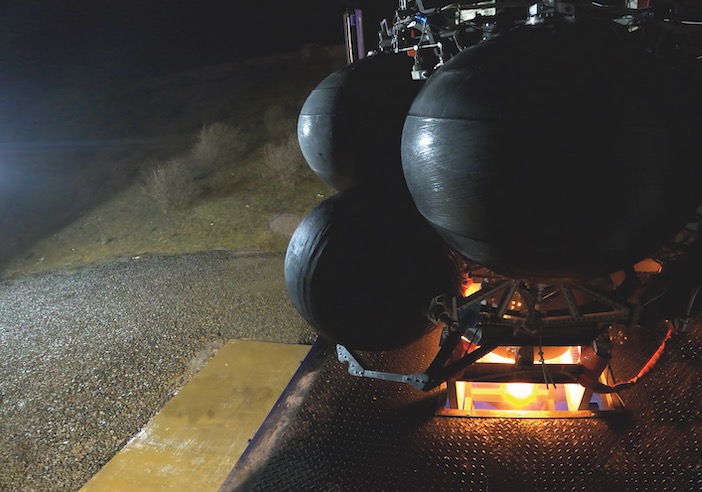
Skyrora’s engine testing facility in Fife, Scotland, where a full series of engine tests have been conducted (Photo: Skyrora)
“It also means our turbo-pump turbine can be operated from decomposed HTP alone, simplifying the overall design. The use of HTP also means our exhaust products contain approximately 40% less CO products than standard LOX / hydrocarbon engines.”
Marlow adds that after running the biofuel through development testing with their engine they were able to achieve “identical performance” to standard kerosene.
Air-breathing ammonia
Another potential biofuel for rocket propulsion is ammonia.
Oxfordshire-based Reaction Engines is using the heat exchanger system developed for its SABRE engine – an air-breathing rocket engine under development – to create an engine fueled by cracked ammonia.
While ammonia is hard to burn, it can be catalytically cracked to produce hydrogen. The idea is to create an engine with an ammonia cracker incorporated into it. Tom Scrope, chief financial officer at Reaction Engines says, “The concept is to crack a portion of the ammonia, separate out the nitrogen and hydrogen and then recombine the hydrogen with the ammonia in situ, using the hydrogen as an igniter for the ammonia.”
Ammonia as a biofuel offers several advantages. Not only is it zero carbon, it is also widely available thanks to use in agricultural fertilizer and is far more stable and easier to handle than hydrogen.
However, while Reaction Engines’ background is in rocket propulsion, the ammonia cracker engine is unlikely to find an application there. Ammonia’s specific impulse cannot compete with current rocket fuel propellants. Furthermore, as a solid fuel it would likely “add dry mass to the launch vehicle causing a corresponding payload penalty,” says Scrope.
“As such, ammonia cracking is better for applications where a true zero-carbon fuel is desired, and efficiency is a stronger driver than system mass – the maritime or aviation industries, for example,” Scrope adds.
‘News of the Day’ content, as reported by public domain newswires.
Source Information (if available)
It appears the above article may have originally appeared on www.aerospacetestinginternational.com and has been shared elsewhere on the internet, repeatedly. News articles have become eerily similar to manufacturer descriptions.
We will happily entertain any content removal requests, simply reach out to us. In the interim, please perform due diligence and place any content you deem “privileged” behind a subscription and/or paywall.
First to share? If share image does not populate, please close the share box & re-open or reload page to load the image, Thanks!